Стальные мостовые конструкции | Решения Mengneng Покрытия
Коррозия — это неизбежное природное явление при эксплуатации стальных мостов. С широким применением стальных конструкций в мостовом строительстве, защита от коррозии становится важной частью работ по сохранению и обслуживанию мостов. В настоящее время в выборе решений по защите от коррозии стальных конструкций как в стране, так и за рубежом, в большинстве случаев используется метод покрытия. Учитывая низкую стоимость покрытия и высокую устойчивость этого метода, в данной статье предлагается инновационное решение для системы защиты от коррозии стальных конструкций мостов.
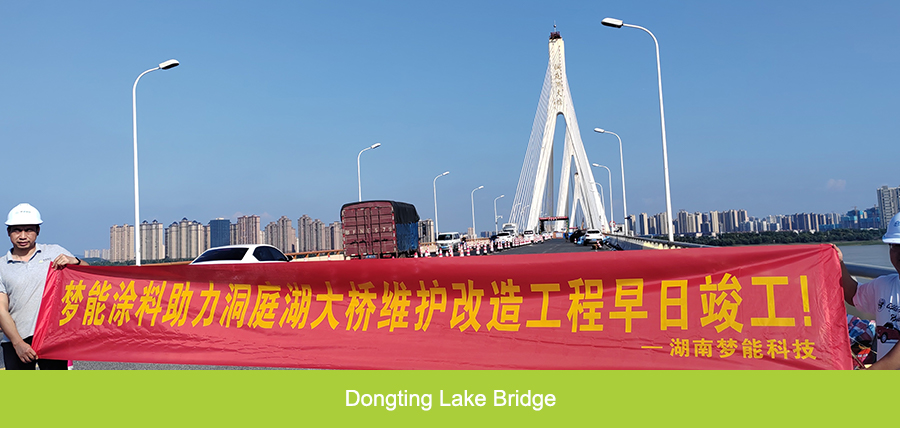
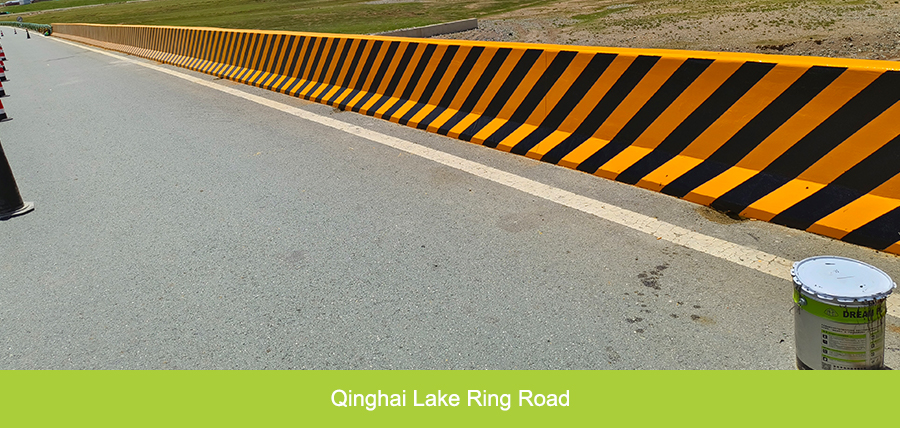
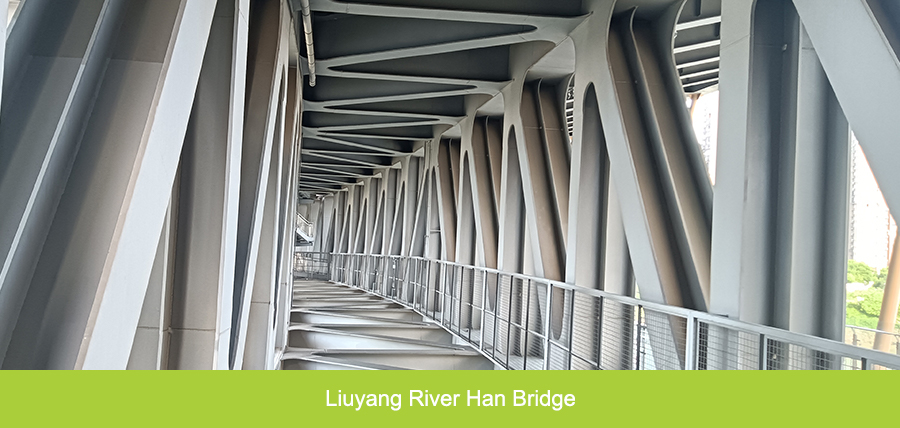
-
Фон коррозии
-
Основные проектные нормы
-
Бетонный мост
-
Мост из стальной конструкции
-
Противопожарная защита кабелей
-
Антиобледенение кабелей
-
Особые подложки
-
Ремонтное покрытие
-
- Защита от коррозии стальных конструкций мостов
-
I. Фон защиты от коррозии сталевых конструкций мостов
Мосты — одно из величайших архитектурных достижений человечества. В определенном смысле, мосты — это не просто вспомогательные сооружения для жизни и общения людей, но и результат человеческой мудрости и силы, представляющие собой произведения искусства, созданные человеком.
Эволюция мостов тесно связана с развитием индустрии покрытий. Развитие этой отрасли связано с применением таких исходных материалов, как смолы, добавки и функциональные пигменты. Успешное использование каждого нового материала приводит к созданию новых продуктов для покрытий, которые, в свою очередь, являются знаковыми продуктами на разных этапах развития покрытия мостов.
II. Опасности коррозии мостов
Строительство мостов принесло огромное удобство для жизни и транспортировки людей, однако сами мосты также подвержены повреждениям, которые требуют ремонта или даже полной реконструкции. Поэтому исследование причин повреждений мостов необходимо для их обслуживания и способствует продлению срока службы мостов. Основными причинами выхода мостов из строя являются плохие материалы, дефекты производства, природные катастрофы, аварии и коррозия. Среди этих причин эксперты сходятся во мнении, что коррозия — одна из основных причин повреждений и выхода мостов из строя.
Металлические материалы мостов, подвергающиеся воздействию внешней среды, легко вступают в химические и электрохимические реакции с окружающими веществами (такими как влага, соль и т. д.). Мосты часто строятся через реки, где влажность окружающей среды обычно высокая, создавая таким образом агрессивную коррозионную среду. Мосты обычно строятся из стали и бетона.
III. Виды коррозии мостов
Мосты строятся с учетом необходимости пересечения рек или морей, что создает сложные условия для коррозии. Из-за огромной территории Китая и разнообразных географических условий коррозия мостов зависит от каждого конкретного местоположения. Поэтому перед проектированием системы защиты от коррозии мостов необходимо тщательно проанализировать коррозионную среду.
(1) Климатические особенности Китая
В зависимости от температуры и влажности в разных районах Китая климат делится на следующие пять типов:
Регион Среднегодовое количество осадков / мм
Среднегодовая влажность / %
Мороз
Температурный диапазон / °C
Северо-запад, Южный Синьцзян, Тибет, Внутренняя Монголия и др.
100~300
<60
-
-30~35
Северный Китай, Северо-восток, Сиань~Шаньдун
500~800
60~80
-
-40~35
Сычуань, Чунцин, бассейн реки Янцзы, Юньнань, Гуйчжоу
1000~1200
>75
Легкое образование конденсата, изморозь
-20~36
Гуандун, Гуанси, бассейн реки Чжухэ
1500~1700
>75
Легкое образование конденсата
-5~40
Хайнань, Гонконг
2000
>75
Легкое образование конденсата
0~40
Тропическая влажная зона: полуостров Лэйчжоу, остров Хайнань и южная часть Тайваня.
Субтропическая влажная зона: южнее Циньлиня, бассейн реки Янцзы, Сычуань, бассейн реки Чжухэ, север Тайваня и Фуцзянь.
Субтропическая сухая зона: Гоби-пустыня к югу от гор Тяньшань в Синьцзяне.
Теплая умеренная зона: север Циньлиня, южная Внутренняя Монголия, Северный Китай и южная часть Северо-востока.
Холодная сухая зона: север Внутренней Монголии и провинция Хэйлунцзян.
(2) Классификация атмосферы коррозионной среды
Коррозия мостов зависит не только от температуры и влажности, но и от коррозионных веществ в атмосфере, таких как хлориды, серные соединения и оксиды азота. Эти вещества образуются из загрязнителей, выбрасываемых в атмосферу (например, автомобильные выбросы или выбросы из котлов), а также из промышленных выбросов и морского климата.
(3) Коррозия в водных средах
Мосты часто строятся через реки и моря, что делает их опоры и балки уязвимыми для воздействия воды. В зависимости от состава воды коррозия в водной среде делится на коррозию пресной воды и коррозию морской воды.
Коррозия пресной воды: Пресная вода содержит мало соли и обычно является кислой. Коррозия пресной воды обычно слабая и вызвана главным образом поглощением кислорода. Однако с увеличением промышленного загрязнения пресной воды коррозия ускоряется. Эти внешние факторы нельзя игнорировать.
Коррозия морской воды: Морская вода — это раствор электролитов, содержащий различные соли. Коррозия морской воды обычно классифицируется в зависимости от взаимодействия материала с морской водой: зона брызг, зона прилива, зона полного погружения и морская грязь. Зона брызг требует наибольших усилий для защиты от коррозии, так как подвергается частым ударам и циклическим воздействиям.
(4) Коррозия в почве
Опоры мостов, как правило, устанавливаются в грунт, и коррозия стали или бетона в почве напрямую влияет на безопасность моста. Факторы, влияющие на коррозию почвы, включают сопротивление, содержание кислорода, соленость, влажность, pH, температуру и микроорганизмы.
-
- Проектирование антикоррозийной защиты мостов
-
I. Основные принципы
Факторы коррозии, влияющие на мосты, различаются в зависимости от окружающей среды, в которой находится мост. Поэтому система антикоррозийных покрытий для мостов должна следовать концепции "индивидуального подхода". С учетом различных факторов при покраске моста основные принципы проектирования покрытия обычно сводятся к следующим четырем ключевым принципам.
1. Полное внимание к коррозионной среде моста
Как упоминалось в предыдущем разделе, на основе различий в атмосферных и химических коррозионных условиях можно классифицировать коррозионную среду моста, ссылаясь на стандарт ISO 12944-2:2017 "Защитные покрытия для стальных конструкций от коррозии — Часть 2: Классификация среды" и стандарт GB/T 15957-1995 "Классификация атмосферной коррозионной среды".
2. Полное внимание к конструкции и рабочим условиям моста, а также различиям в типах и условиях конструкции
Требования к обработке поверхности и нанесению покрытия сильно различаются и являются важной основой для индивидуального проектирования покрытия. Эти факторы включают:
● Стальная или бетонная конструкция;
● Типы конструкций моста — стальной коробчатый балка, стальной плитный балка, стальной решетчатый балка, стальной трубный арк;
● Особенности канатов и ветровых клапанов на висячих мостах, мостах с наклонными стойками и арочных мостах;
● Рабочие условия и характеристики микроокружения каждой части моста;
● Требования к внешнему виду и цвету моста;
● Координация между производственным процессом моста и работой по нанесению покрытия.
3. Полное внимание к уровню строительной технологии
Защитные функции покрытий включают катодную защиту, ингибирование коррозии и экранирование. Строительная технология напрямую влияет на обработку поверхности подложки, качество образования пленки покрытия и, соответственно, на эффективность защиты покрытия. Например, если цинкосодержащая краска наносится на стальную поверхность, которая не достигла уровня Sa2.5 обработки, то эффект катодной защиты не будет удовлетворительным. Поэтому современная покраска мостов акцентирует внимание на обработке подложки, выборе качественных защитных покрытий, правильном проектировании системы покрытий, строгом контроле качества при выполнении работ и усилении обслуживания в процессе эксплуатации для обеспечения и продления срока службы моста.
4. Полное внимание к инвестиционным ограничениям
Как и в любом другом проектировании, проектирование покрытия должно внедрять подход "Анализа экономических затрат за весь жизненный цикл" (LCCA) (подробности см. в разделе II этой главы); контроль инвестиций в пределах допустимых рамок является важным для реализации.
II. Срок службы защитных покрытий от коррозии
Система защитных покрытий должна быть выбрана в зависимости от ожидаемого срока службы моста. Как правило, для крупных новых мостов, если качество строительства покрытия соответствует стандартам и проводится регулярное обслуживание покрытия после завершения моста, срок службы защитной системы покрытия для крупных стальных мостов обычно составляет 25 лет. Некоторые крупные новые мосты в Китае требуют, чтобы проектный срок службы защитных покрытий был 25-30 лет. Особенно в недавно опубликованном стандарте ISO 12944-1:2017 прямо указано, что максимальная долговечность защитных покрытий для стальных конструкций составляет более 25 лет, что стимулирует повышение требований к проектированию защитных систем покрытий для новых мостов.
III. Содержание проектирования защитного покрытия
Документ по проектированию защитного покрытия должен включать в себя следующие основные моменты:
1. Проектный срок службы покрытия
Определение срока службы покрытия проектируемого объекта;
2. Анализ коррозионной среды
Анализ коррозионной среды проектируемого объекта (C1~C5, CX, Im1 и т.д.) в соответствии с требованиями стандартов ISO 12944-2:2017 и GB/T 15957-1995;
3. Ссылки на стандарты
Включает такие стандарты, как ISO 12944-2017, Q/CR 749-2020, JT/T 722-2021, HG/T 3668-2009 и т. д.;
4. Система покрытия
На основе местоположения покрытия, ссылки на соответствующие стандарты для проектирования системы покрытия;
5. Технические характеристики продуктов
На основе проектируемой системы покрытия ссылаться на соответствующие стандарты для определения технических характеристик покрытия;
6. Процесс нанесения покрытия
Обычно включает в себя обработку конструкции, обработку поверхности, очистку поверхности, проверку окружающей среды и операционные работы по нанесению покрытия. Обработка конструкции включает устранение дефектных частей конструкции моста, таких как острые углы и кромки; обработка поверхности включает методы, такие как дробеструйная обработка, пескоструйная обработка, механическая или ручная шлифовка, кислотная мойка; очистка поверхности включает удаление пыли, масла, жиров и солей с поверхности; проверка окружающей среды включает проверку условий нанесения покрытия, таких как температура стали, температура окружающей среды, влажность, точка росы, вентиляция, освещение, безопасность и другие факторы; операционные работы включают выбор метода нанесения покрытия и различных условий в соответствии с проектом.
7. Контроль качества и приемка
Проведение проверки качества до и после нанесения покрытия в соответствии с требованиями проектирования покрытия, включая проверку шероховатости поверхности и чистоты до нанесения покрытия, а также проверку толщины покрытия и прочности на отрыв после нанесения покрытия. Завершить проверку качества и приемку.
IV. Проектирование цветовой схемы покрытия моста
На сегодняшний день мосты уже не являются просто традиционными средствами для облегчения движения. Многие мосты представляют собой имидж города и отражают его особенности. Например, стальная коробчатая балка Моста через реку Янцзы Руньянга окрашена в металлический алюминиевый цвет, пересекающий мощный Янцзы, как серебристая галактика; канаты моста Шаньтоу Каиши искусно окрашены в оранжево-желтый цвет, и, вдали, они напоминают лучи солнца, разливающиеся по зеленым волнам; мост Сяовань в Юньнани использует ледяной серый цвет, гармонично сливаясь с окружающими зелеными горами и водой, усиливая туристическую привлекательность. Поэтому мосты стали красивыми линиями пейзажа для городов и регионов. В результате владельцы все больше обращают внимание не только на защитные характеристики, но и на внешний вид моста, особенно на выбор цвета защитного покрытия.
Однако проектирование цвета — это не простая задача. Во-первых, восприятие цвета человеком очень сложно. Некоторые цвета создают у людей чувство покоя и комфорта; наоборот, некоторые цвета вызывают беспокойство и напряжение. Для водителей, пересекающих мост, цвет также связан с безопасностью. Во-вторых, цвет оказывает значительное влияние на стоимость и стойкость продукта. Некоторые цвета, такие как ярко-красный или ярко-желтый, могут использовать недорогие азокрасители, но имеют плохую стойкость к погодным условиям, что не позволяет достичь долгосрочной защиты; использование других пигментов может значительно увеличить стоимость. Поэтому проектирование цвета стало важной частью проектирования защитного покрытия моста. Дизайнеры должны учитывать не только требования владельца, но и вопросы безопасности, стоимости и стойкости к погодным условиям.
В общем, проектирование цвета должно соответствовать принципам гармонии между эстетикой процесса, свойствами покрытия, технической экономикой и окружающей средой.
- Основные нормативы: ISO 12944
-
I. Основные стандарты
Дизайн покрытия мостов должен в полной мере учитывать влияние атмосферных коррозионных условий. ISO 12944-2:2017 "Системы защитных покрытий для стальных конструкций от коррозии — Часть 2: Классификация окружающей среды" и GB/T 15957-1995 "Классификация атмосферной коррозионной агрессивности" являются наиболее широко используемыми и практическими стандартами в проектировании покрытий. Конкретные методы классификации можно найти в разделе "Классификация атмосферных коррозионных условий" этой главы.
II. Стандарты отрасли защиты мостов от коррозии
(1) Стандарты железнодорожной отрасли
Ранее в Китае для защиты стальных мостов от коррозии были установлены четыре отраслевых стандарта. Стандарт TB/T 2486-1994 "Оценка деградации покрытия железнодорожных стальных балок" определяет типы деградации, уровни деградации и методы оценки покрытия железнодорожных стальных балок. Он применяется для оценки состояния, качества и деградации покрытий на стальных балках, а также классификации покрытий на стальных мостах и других стальных конструкциях. Стандарт TB/T 1527-2004 "Защитные покрытия для железнодорожных стальных балок" устанавливает технические требования, методы испытаний и правила инспекции для защитных покрытий железнодорожных мостов. Он применяется к первичной покраске, повторной покраске после деградации покрытия и обслуживанию железнодорожных мостов. Стандарты TB/T 2772-1997 "Технические условия поставки антикоррозионных грунтовок для железнодорожных мостов" и TB/T 2773-1997 "Технические условия поставки финишных и промежуточных красок для железнодорожных мостов" определяют классификацию, технические требования, методы испытаний, правила инспекции, упаковку, маркировку, транспортировку и хранение антикоррозионных грунтовок, промежуточных красок и финишных красок для железнодорожных мостов. Эти стандарты применяются к новым покрытиям стальных балок, повторным покрытиям стальных балок в эксплуатации и покрытиям других стальных конструкций. В 2011 году стандарты TB/T 2772-1997 и TB/T 2773-1997 были отменены и объединены в TB/T 1527-2011 "Защитные покрытия и технические условия поставки красок для железнодорожных стальных мостов".
В 2020 году оригинальный стандарт Министерства железных дорог TB/T 1527-2011 был также отменен и заменен новым стандартом предприятия China Railway Corporation Q/CR 749-2020 "Защитные покрытия и краски для стальных конструкций и компонентов железнодорожных мостов". Этот стандарт разделен на три части: часть 1 - стальные мосты, часть 2 - опоры, часть 3 - пешеходные стальные балки и вспомогательные стальные конструкции. Он устанавливает системы защитных покрытий, технические требования, методы испытаний, правила инспекции, а также упаковку, маркировку, транспортировку и хранение для этих трех типов конструкций. Стандарт применяется к первичной покраске, повторной покраске после деградации покрытия и обслуживанию, а также к антикоррозионной грунтовке, промежуточной краске и финишной краске, используемым в покрытиях.
(2) Стандарты химической отрасли
Стандарт HG/T 3656-1999 "Покрытия для стальных мостов" делит покрытия для стальных мостов на обычные и долговечные типы в зависимости от срока службы. Он устанавливает технические требования, методы испытаний, правила инспекции, а также упаковку, маркировку, транспортировку и хранение для антикоррозионных грунтовок, промежуточных красок и финишных красок для этих двух типов продукции. В приложении приведены общие разновидности этих продуктов и описаны несколько реальных систем применения.
(3) Стандарты транспортной отрасли
JT/T 722-2008 Технические условия для покрытий стальных конструкций мостов для автодорог
JT/T 694-2007 Технические условия для антикоррозийных покрытий главных канатов подвесных мостов
JT/T 695-2007 Технические условия для покрытий поверхности бетонных мостов
Из этих стандартов, JT/T 722-2008 был пересмотрен в 2020 году. Новый пересмотренный стандарт отражает передовые и перспективные технологии покрытий в области транспортных мостов. Кроме того, он предоставляет методы и основания для внедрения новых продуктов, технологий и процессов. Пересмотр стандарта учитывает экономию и экологичность долговечности мостов, а также успехи и неудачи практики защитных покрытий мостов в Китае, а также международный опыт, особенно новый ISO 12944 и международные стандарты защиты от коррозии мостов. Стандарт JT/T 694-2007 применяется к антикоррозийным покрытиям для главных канатов подвесных мостов. В дополнение к определению соответствующих терминов и определений, он также описывает системы материалов для покрытия канатов, процессы строительства, показатели производительности материалов и требования безопасности, санитарии и охраны окружающей среды. Стандарт JT/T 695-2007 устанавливает системы покрытия и показатели производительности для бетонных мостов в различных коррозионных условиях, а также требования к строительству покрытий, приемке, безопасности, санитарии и охране окружающей среды. Стандарты JT/T 694-2007 и JT/T 695-2007 будут пересмотрены в ближайшие годы.
-
- Решение по восстановлению и антикоррозийной защите бетонных мостов
-
I. Реновация бетонных мостов
Так как бетон является сильно щелочным строительным материалом, необходимо, чтобы защитные покрытия для бетона обладали хорошей щелочестойкостью, адгезией и водоотталкивающими свойствами. Кроме того, само покрытие должно иметь отличную стойкость к атмосферным воздействиям и долговечность. Для бетонных конструкций на прибрежных мостах поверхностное покрытие должно обладать выдающимися стойкостью к атмосферным воздействиям, устойчивостью к солнечной радиации и ультрафиолетовому разрушению, стойкостью к солевым аэрозолям и коррозии морской атмосферы, не подвергаясь значительному поседению, изменению цвета, отслаиванию или трещинам в течение срока эффективной защиты.
В соответствии с техническими нормативами для защиты бетона от коррозии в портовых сооружениях (JTJ275-2001), нормативами по проектированию защиты от коррозии промышленных зданий (GB50046-95) и строительными нормативами по защите от коррозии и приемке работ (GB50212-2002) эпоксидные покрытия, полиуретановые покрытия, хлорированные резиновые покрытия, виниловые покрытия и акриловые покрытия считаются подходящими типами покрытий. Исходя из отечественного и зарубежного опыта применения защитных покрытий для бетона на мостах, рекомендуется использовать следующие покрытия для достижения хороших результатов.
A1: Рекомендуемая система покрытия DreamCover для атмосферных зон поверхности моста, крышек опор, опорных частей, ограждений и дорожных покрытий
Основание проектирования ISO12944-5:2017 Системы защитных покрытий для защиты от коррозии стальных конструкций Условия окружающей среды C4 Высокий; Внешние: Средняя соленость в промышленных и прибрежных районах Срок службы VH сверхдолгий Обработка поверхности ISO 8501-1 St2: Тщательная ручная и механизированная очистка стали от ржавчины, поверхность должна быть свободна от видимых жировых пятен и грязи, без слабо прикрепленных оксидных пленок, ржавчины или слоев краски. Области покрытия Атмосферные зоны мостов, крышки опор, мостовые плиты, опоры, ограждения, покрытия Покрытие Тип покрытия Наименование покрытия Цвет Разбавитель Соотношение A:B Толщина пленки (μm) Первое покрытие DreamCover Графеновый грунт с низкой поверхностной обработкой DreamCover 220 Gns Серый, светло-серый, красно-коричневый, белый, полуглянец Специальный разбавитель для графена DreamThinner 17 Gns 25:5 220 Второе покрытие DreamDur Фторкарбоновое покрытие DreamDur 22F Пожалуйста, используйте цвета по RAL и национальным стандартам Специальный разбавитель DreamThinner X 22.73:2.27 80 Итог 300 A2: Рекомендуемая система покрытия DreamCover для реновации подводных частей опор мостов и зон чередования сухости и влажности
Основание проектирования ISO12944-5:2017 Системы защитных покрытий для защиты от коррозии стальных конструкций Условия окружающей среды Im1; Пресная вода: Установленные сооружения на реках, гидроэлектростанции Срок службы VH сверхдолгий Обработка поверхности ISO 8501-1 St2: Тщательная ручная и механизированная очистка стали от ржавчины, поверхность должна быть свободна от видимых жировых пятен и грязи, без слабо прикрепленных оксидных пленок, ржавчины или слоев краски. Области покрытия Подводная часть опор мостов, зоны чередования сухости и влажности Покрытие Тип покрытия Наименование покрытия Цвет Разбавитель Соотношение A:B Толщина пленки (μm) Первое покрытие DreamCover Графеновый грунт с стекловолоконными чешуйками DreamCover 152 Gns Черный, желтый Специальный разбавитель для графена DreamThinner 17 Gns 23.3:3.7 300 Итог 300
- Новый проект для бетонных мостов
-
I. Угрозы коррозии бетонных мостов
Поскольку бетон — это сильно щелочной строительный материал, эксперты DreamCoatings считают, что антикоррозийное покрытие для бетона должно обладать хорошей стойкостью к щелочам, адгезией и водоотталкивающими свойствами. Кроме того, покрытие должно иметь хорошую стойкость к погодным условиям и долговечность. Для бетонных мостов, расположенных в прибрежных зонах, поверхность покрытия должна обладать отличной стойкостью к погодным условиям, стойкостью к ультрафиолетовому излучению и солнечному воздействию, устойчивостью к соляным брызгам и морской коррозии, а также не должна проявлять сильную побелку, обесцвечивание, отслаивание или трещины в период эффективной защиты.
Коррозия армированного стального каркаса
Эрозия хлоридными ионами: Хлоридные ионы из морской воды, соленых почв, противогололедных солей и т.д. могут проникать в бетон, разрушая пассивную пленку на поверхности арматуры, что приводит к коррозии стали.
Карбонизация: Диоксид углерода (CO2) в воздухе реагирует с гидроксидом кальция (Ca(OH)2) в бетоне, образуя карбонат кальция (CaCO3), что снижает pH бетона и уменьшает его защитные свойства для стали.
Влага и кислород: Сталь, подвергшаяся воздействию влаги и кислорода, подвержена электрохимической коррозии.
Ухудшение качества бетона
Карбонизация: Карбонизация бетона не только снижает pH бетона, уменьшая защиту стали, но и ведет к снижению прочности бетонной конструкции.
Цикл замораживания и оттаивания: В холодных районах вода внутри бетона замерзает и расширяется. Повторяющиеся циклы замораживания и оттаивания приводят к образованию микро-трещин внутри бетона, что в итоге приводит к отслаиванию.
Сульфатная атака: Когда бетон вступает в контакт с грунтовыми водами или почвой, содержащими сульфаты, ионы сульфата вступают в реакцию с ионами кальция в бетоне, образуя расширяющиеся продукты, которые вызывают набухание бетона и его разрушение.
Механические повреждения
Физические воздействия: Внешние механические воздействия, такие как столкновение с транспортными средствами и падение камней, могут повредить бетон.
Вибрации: Долговременные нагрузки от движения транспорта и вибрации также могут привести к усталостному повреждению бетона.
Химическая эрозия
Кислотные среды: В некоторых промышленных районах или в условиях кислотных дождей бетон может подвергаться эрозии кислотными веществами.
Другие химикаты: Определенные растворители, масла и другие химикаты также могут повредить бетон.
Микробная коррозия
Микробная коррозия: В определенных условиях микробная активность может ускорить процесс коррозии бетона и арматуры.
Эти угрозы коррозии влияют на безопасность и долговечность бетонных мостов, поэтому необходимо принимать соответствующие защитные меры для продления срока службы моста, такие как использование высококачественного бетона, применение катодной защиты и регулярные осмотры и обслуживание.
II. Антикоррозионные решения для бетонных мостов с использованием графеновых покрытий
Рекомендованный стандарт: JT/T 695-2007 Технические условия для покрытия поверхностей бетонных мостовых конструкций от коррозии
Бетонные мосты классифицируются в основном по их конструкции и компонентам. Обычно бетонный мост состоит из следующих основных компонентов:
Проезжая часть: Проезжая часть — это платформа на мосту, предназначенная для поддержания транспортных средств и пешеходов. Как правило, она изготавливается из асфальта, бетона или стальных плит для обеспечения прочности и долговечности.
Опоры: Опоры являются точками соединения моста с его фундаментом и предназначены для поддержания веса моста и нагрузок, передавая эти силы на фундамент. Опоры обычно изготавливаются из резины или стали для обеспечения хорошей грузоподъемности и амортизирующих свойств.
Главные балки: Главные балки являются основными несущими элементами моста и отвечают за несение нагрузки на мосту и передачу этой нагрузки на опоры. Обычно они изготавливаются из бетона, стали или преднапряженного бетона для обеспечения высокой прочности и долговечности.
Опоры мостовых арок: Опоры мостовых арок — это вертикальные поддерживающие структуры моста, используемые для поддержания главных балок и нагрузки на мост. Опоры обычно изготавливаются из бетона или стали, обеспечивая хорошую грузоподъемность и структурную устойчивость.
Фундамент: Фундамент — это структура, которая поддерживает мост на земле. Обычно фундаменты изготавливаются из бетона или стали, обеспечивая достаточную прочность и стабильность для несения нагрузок на мост.
Кроме того, мост может включать другие компоненты, такие как соединительные балки, опорные платформы, колонны, балочные балки, опорные прокладки и т. д. Эти части работают вместе, чтобы обеспечить безопасность и стабильность моста.
B1. Рекомендуемые антикоррозийные решения для мостовых арок и опор в атмосферных условиях, крыши, платформы и дорожное покрытие
Основы проектирования ISO12944-5:2017 Защитные покрытия для стальных конструкций от коррозии Условия окружающей среды C4 Высокая; Внешние: Средняя соль, промышленные и прибрежные районы Проектируемый срок службы VH Сверхдолговечный Обработка поверхности ISO 8501-1 St2: Тщательное удаление ржавчины вручную и с помощью электроинструментов с стальных поверхностей Область покрытия Мосты в атмосфере, крыши, платформы, опоры и дорожное покрытие Покрытие Тип покрытия Название покрытия Цвет Растворитель Соотношение A:B Толщина пленки (мкм) Первое покрытие DreamCover Герметик для бетона DreamCover Clear 600 Прозрачный Эпоксидный растворитель DreamThinner 17 15:3 40 Второе покрытие DreamCover Графеновый праймер DreamCover 220 Gns Серый, светло-серый, красно-коричневый, белый полуглянец Графеновый растворитель DreamThinner 17 Gns 25:5 180 Третье покрытие DreamDur Фтороуглеродное покрытие DreamDur 22F Поддерживает RAL, национальное стандартное цветовосприятие Специальный растворитель DreamThinner X 22.73:2.27 80 Итого 300 B2. Рекомендуемые антикоррозийные решения для подводных и зон с попеременной влажностью для опор мостов
Основания проектирования ISO12944-5:2017 Защитные покрытия для стальных конструкций от коррозии Условия окружающей среды Im1; Пресная вода: Установки на реках, гидроэлектростанции Проектируемый срок службы VH Очень долгий срок службы Обработка поверхности ISO 8501-1 St2: Тщательное удаление ржавчины вручную и с помощью электрических инструментов с металлических поверхностей должно быть без видимого жира и грязи, и не должно быть легко отслаивающихся окисленных слоев, ржавчины или краски. Места покрытия Подводные части мостовых опор, зоны чередования влажности Покрытие Тип покрытия Название покрытия Цвет Растворитель Соотношение A:B Толщина пленки Первое покрытие DreamCover DreamCover Clear 600 Гидроизоляция для бетона Прозрачный Эпоксидный растворитель DreamThinner 17 15:3 40 Второе покрытие DreamCover Графеновый грунт с стеклянными чешуйками DreamCover 152 Gns Черный, Желтый Графеновый растворитель DreamThinner 17 Gns 23.3:3.7 300 Итого 340
-
- Решение по новому строительству мостов из стальной конструкции
-
I. Corrosion Facing Steel Structure Bridges
Steel structure bridges stand outdoors day and night, exposed to sunlight and rain. Due to the effects of various media, corrosion is likely to occur. If effective anti-corrosion methods are not applied to protect the steel structure, the service life of the steel bridge will significantly decrease, or it may even be prematurely scrapped.
1. Uniform Corrosion
Uniform corrosion is the most common form of corrosion. Its main characteristic is that corrosion is distributed across the entire metal surface, causing a uniform reduction in the thickness of the metal. Although uniform corrosion results in significant metal loss, it is not particularly dangerous. Since the corrosion rate is uniform, it is easy to predict and prevent. With strict engineering design and reasonable anti-corrosion measures, steel bridges generally will not experience sudden corrosion accidents.
2. Pitting Corrosion
In suitable environmental media, most of the steel surface remains unaffected by corrosion, but localized pits or microzones appear due to selective corrosion of the metal. As time goes on, the pits develop deeper. This form of corrosion is called pitting. Pitting corrosion is generally caused by Cl- ions adsorbing at defects in the metal surface film. For example, a suspension bridge in Guangdong completed in December 1988 experienced the sudden fracture of a cable in January 1995. Analysis of the corrosion products found that they contained 0.1% Cl- and 0.1% SO42-. The fracture was mainly caused by pitting corrosion due to Cl-.
3. Crevice Corrosion
Crevice corrosion occurs when a metal is in contact with another metal or non-metallic material, creating a crevice where corrosion occurs in the presence of a corrosive medium. It mainly occurs in places such as riveted joints, bolted connections, screw joints, and between non-metallic flanged gaskets and metal materials.
II. Anti-corrosion Coating for Bridge Steel Structures
Commonly used anti-corrosion measures for steel structures can be divided into two categories: one is mechanical isolation, where inert materials are applied to cover the steel surface to isolate corrosion media like water and oxygen; the other is based on electrochemical corrosion principles, where the steel structure's potential is artificially increased to protect it. Based on these principles, commonly used anti-corrosion methods include flame spraying, hot-dip galvanizing, coating, and arc spraying composite coatings.
Using coatings for anti-corrosion protection of steel bridges has been practiced for over 100 years. Through continuous development and extensive application, a series of dedicated bridge coatings have now been formed. Since no coating can simultaneously provide isolation, UV resistance, and cathodic protection, the coating system for steel bridges typically consists of a comprehensive anti-corrosion system, including primer, intermediate coating, and topcoat, which work together through mechanical shielding, passivation, and cathodic protection.
A1. Wind Faring and Inner Surface of Structural Stays
Wind faring is a special structure in the cross-section of a bridge steel box girder. It is composed of the top and bottom plates and web plates on both the upstream and downstream sides to improve the aerodynamic performance of the section and enhance the wind stability of the bridge. Wind faring on bridges is designed to reduce the resonance effects caused by strong winds on the bridge deck.
Design Basis ISO12944-5:2017 Protective Coating Systems for Steel Structures Environment C5 Very High; External: Industrial areas with high humidity, harsh weather, and high salinity coastal regions Design Life VH Ultra-long-term Surface Treatment ISO 8501-1 Sa2.5: Very thorough shot blasting or abrasive blasting. The steel surface should be free of visible grease, dirt, mill scale, rust, paint coatings, etc. Any remaining traces should be only light spots or streaks. Coating Area Wind faring, inner surface of structural stays Coating Paint Type Paint Name Color Thinner A:B Ratio Film Thickness (μm) First Coat DreamZinc Graphene Zinc Powder Primer DreamZinc 30 Gns Graphite Grey Graphene Thinner DreamThinner 17 Gns 30.8:3.2 80 Second Coat DreamCover Epoxy Zinc Rich Intermediate Coat DreamCover 150 Light Grey Mica Oxide Epoxy Thinner DreamThinner 17 25.2:6.8 140 Third Coat DreamDur Acrylic Polyurethane Topcoat DreamDur 550 Custom RAL, National Standard Colors Polyurethane Thinner DreamThinner 10 21.4:3.6 80 Total 300 *The above solution uses the fourth-generation graphene coating solution. Please contact us for other options.
A2, External Surface of Auxiliary Facilities
Bridge auxiliary facilities include the bridge deck system, expansion joints, bridge head slabs, cone slopes, drainage facilities, etc.
Design Basis ISO12944-5:2017 Protective Coating Systems for Steel Structures against Corrosion Environmental Conditions C5 very high; External: High humidity and severe weather industrial areas and coastal areas with high salinity Design Service Life VH ultra-long service life Surface Treatment ISO 8501-1 Sa2.5: Very thorough blasting or shot blasting. The steel surface must be free of visible grease, dirt, scale, rust, paint coatings, or other contaminants. Any remaining marks should only be light spot or strip marks. Coated Areas Bridge deck system, expansion joints, bridge head slabs, cone slopes, drainage facilities, etc. Coating Coating Type Coating Name Color Compatible Thinner A:B Ratio Film Thickness (μm) First Coat DreamCover Graphene Low Surface Treatment Primer DreamCover 220 Gns Grey, Light Grey, Red-Brown, White Semi-gloss Graphene Thinner DreamThinner 17 Gns 25:5 220 Second Coat DreamDur Fluorocarbon Topcoat DreamDur 22F Supports L'Oréal and National Color Standards Special Thinner DreamThinner X 22.73:2.27 80 Total 300 * The above solution uses the fourth-generation graphene coating solution. For other solutions, please contact us.
A3. Стальной коробчатый балка, стальной якорный ящик, соединение узловых соединений
Стальной коробчатый балка: Стальной коробчатый балка — это тип мостовой конструкции с поперечным сечением, напоминающим коробку, изготовленный из сварных стальных пластин. Он используется в основном для строительства мостов с большими пролетами благодаря своей жесткости, высокой грузоподъемности, легкости и отличным сейсмическим характеристикам.
Стальной якорный ящик: Стальной якорный ящик — это конструкция, используемая для фиксации главных канатов или наклонных канатов в подвесных или наклонных мостах. Он в основном несет натяжение, передаваемое от главных канатов или наклонных канатов, и равномерно распределяет эти силы на башни моста или опоры.
Узловой соединитель: Узловой соединитель — это соединительный элемент, используемый в узлах стальных конструкций, предназначенный для соединения элементов в нескольких направлениях, таких как стержни в конструкции фермы. Это высокопрочный способ соединения, способный выдерживать большие осевые и сдвиговые силы.
Основание проектирования ISO12944-5:2017 Системы защитных покрытий для стальных конструкций от коррозии Условия эксплуатации C5 очень высокий; Внешняя среда: промышленные районы с высокой влажностью, суровыми погодными условиями и прибрежные районы с высокой соленостью. Срок службы VH сверхдолгий Обработка поверхности ISO 8501-1 Sa2.5: Очень тщательная абразивная или дробеструйная очистка. Поверхность стали должна быть свободна от видимых следов жира, грязи, окалины, ржавчины, лакокрасочных покрытий и других загрязнителей. Остаточные следы должны быть только точечными или полосовыми легкими пятнами. Область нанесения покрытия Стальной коробчатый балка, стальной якорный ящик, соединения узловых соединений Покрытие Тип краски Название краски Цвет Совместимый растворитель Соотношение A:B Толщина покрытия (μm) Первый слой DreamZinc Холодное напыление цинка DreamZinc 96 Цинковый серый Растворитель для холодного напыления цинка DreamThinner 16 AX 30:0 100 Второй слой DreamCover Герметик для холодного напыления цинка DreamCover 167 Серый, матовый Эпоксидный растворитель DreamThinner 17 27:4.5 200 Итого 300 *Приведенное решение использует третье поколение покрытия холодным напылением цинка. Для других решений, пожалуйста, свяжитесь с нами.
A4. Коробчатая балка, внешняя поверхность соединителей узлов
Коробчатая балка: Коробчатая балка — это конструкция с закрытым сечением, обычно используемая в проектировании мостов с большими пролётами, таких как мосты с непрерывными балками или консольные мосты. Коробчатая балка состоит из верхней и нижней плит и боковых стенок, образующих закрытую коробчатую структуру.
Соединитель узла: Соединитель узла представляет собой элемент, используемый в стальных конструкциях для соединения компонентов в нескольких направлениях, как, например, элементы в стержневой конструкции. Это высокопрочное соединение, способное выдерживать большие осевые и сдвиговые нагрузки.
Основания проектирования ISO12944-5:2017 Системы защитных покрытий для стальных конструкций от коррозии Экологические условия C5 очень высокие; внешняя среда: промышленные районы с высокой влажностью, суровыми погодными условиями и высокими солёными прибрежными регионами. Срок службы VH сверхдолгий Обработка поверхности ISO 8501-1 Sa2.5: Очень тщательная очистка с помощью струйной или пескоструйной обработки. Поверхность стали должна быть свободна от видимых следов масла, грязи, окалины, ржавчины, краски и других загрязнений, оставшиеся следы должны быть в виде лёгких точечных или полосовых пятен. Места покраски Коробчатая балка, внешняя поверхность соединителей узлов Покрытие Тип краски Название краски Цвет Растворитель Соотношение A:B Толщина покрытия (мкм) Первый слой DreamZinc Холодное цинкование DreamZinc 96 Цинковый серый Растворитель для холодного цинка DreamThinner 16 AX 30:0 80 Второй слой DreamCover Герметик для холодного цинка DreamCover 167 Серый, матовый Эпоксидный растворитель DreamThinner 17 27:4.5 120 Общая сумма 200 *Предложенное решение использует покрытие холодного цинка третьего поколения. Для других решений, пожалуйста, свяжитесь с нами.
A5. Внутренняя поверхность коробчатой балки
Обработка коррозии внутренней поверхности коробчатой балки также имеет большое значение, поскольку внутри балки скапливается влага, и она плохо вентилируется, что делает её особенно подверженной коррозии.
Основания проектирования ISO12944-5:2017 Системы защитных покрытий для стальных конструкций от коррозии Экологические условия C5 очень высокие; внешняя среда: промышленные районы с высокой влажностью, суровые погодные условия и высокие солёные прибрежные районы. Срок службы VH сверхдолгий Обработка поверхности ISO 8501-1 Sa2.5: Очень тщательная очистка с помощью струйной или пескоструйной обработки. Поверхность стали должна быть свободна от видимых следов масла, грязи, окалины, ржавчины, краски и других загрязнений, оставшиеся следы должны быть в виде лёгких точечных или полосовых пятен. Места покраски Внутренняя поверхность коробчатой балки Покрытие Тип краски Название краски Цвет Растворитель Соотношение A:B Толщина покрытия (мкм) Первый слой DreamZinc Холодное цинкование DreamZinc 96 Цинковый серый Растворитель для холодного цинка DreamThinner 16 AX 30:0 80 Второй слой DreamCover Герметик для холодного цинка DreamCover 167 Серый, матовый Эпоксидный растворитель DreamThinner 17 27:4.5 120 Общая сумма 200 *Предложенное решение использует покрытие холодного цинка третьего поколения. Для других решений, пожалуйста, свяжитесь с нами.
-
- Противопожарная защита для подвесных мостов
-
I. Влияние пожара на основные кабели мостов
С увеличением числа транспортных средств и объема движения, аварии с пожарами на мостах с кабельной опорой случаются все чаще. Кабели, как важный несущий элемент системы кабельной опоры мостов, несмотря на хорошие механические характеристики и стойкость к погодным условиям, имеют плохую огнестойкость таких материалов, как высокопрочные стальные проволоки, полиэфирные волокна, оболочки PE и антикоррозийные покрытия. Когда на мостовой части происходит пожар (особенно при аварии с бензовозом), оболочка PE может легко загореться, температура стальной проволоки продолжает повышаться, антикоррозийный слой отслаивается, а характеристики стали ухудшаются, что создает серьезную угрозу для безопасной эксплуатации моста, как показано в Таблице 1 и на Рисунке 1. В настоящее время в отрасли еще не разработаны стандарты проектирования противопожарной защиты для несущих стальных конструкций, и нет соответствующих руководящих принципов по защите таких важных стальных элементов, как кабели, в условиях пожара.
Подвесные мосты, благодаря своей уникальной конструкции, являются важной частью современной мостовой инженерии. Однако эта конструкция сталкивается с серьезными угрозами безопасности при воздействии огня. Основные кабели, являясь ключевым элементом подвесных мостов, имеют критические требования по противопожарной защите для обеспечения общей безопасности моста. В этой статье предлагается исследование и предложение комплексного решения для противопожарного покрытия, чтобы улучшить огнестойкость основных кабелей при возникновении пожара.
1. Проблемы с пожарной безопасностью основных кабелей подвесных мостов
Основные проблемы, с которыми сталкиваются подвесные мосты в условиях пожара, включают:
Термическое повреждение основных кабелей: Высокие температуры могут привести к потере прочности основных кабелей или даже их разрушению.
Структурная стабильность: Высокие температуры, возникающие в ходе пожара, могут повлиять на общую структурную стабильность моста.
Трудности спасательных операций: Высота и пролёт подвесного моста усложняют тушение пожара и проведение спасательных операций.
Таблица 1: Аварии с пожаром на кабельных мостах
№ Дата аварии Название моста Причина пожара 1 Апрель 2009 года Мост через реку Вуху Пожар от легкового автомобиля 2 Октябрь 2011 года Мост в Нанкине Самовозгорание грузовика 3 Ноябрь 2011 года Мост в Харбине Множество возгораний автомобилей 4 Октябрь 2014 года Мост в Гуанчжоу Самовозгорание грузовика 5 Январь 2014 года Мост на шоссе Чжэншao Пожар бензовоза 6 Июнь 2017 года Мост на Гуанкунь Самовозгорание грузовика 7 Март 2018 года Мост в Хубэе Самовозгорание грузовика 8 Июль 2020 года Мост в Ухане Самовозгорание грузовика 9 Июль 2021 года Мост в Нанкине Пожар бензовоза 10 Сентябрь 2022 года Мост в Аньхуе Пожар силикогеля
II. Проблемы традиционных огнеупорных материалов
Материалы для огнезащиты кабелей мостов должны удовлетворять требованиям как по огнестойкости, так и по теплоизоляции. Кроме того, чтобы удовлетворить потребности в обертывании кабелей, материалы должны обладать определенной гибкостью. Как полупостоянная мера защиты моста, система огнезащиты кабелей должна также учитывать требования устойчивости к воздействию внешней среды, такие как устойчивость к УФ-старению, водоотталкивающие свойства, стойкость к кислотным дождям и способность адаптироваться к вибрациям мостовой конструкции.
После обширных исследований и сравнений, материалы с потенциалом для защиты кабелей от огня и теплоизоляции в основном включают войлочные огнеупорные материалы, такие как войлок из базальтового волокна, войлок из керамических волокон или аэрогель для теплоизоляции. Войлочные изделия также требуют дальнейшей классификации на основе таких параметров, как механическая прочность, термостойкость и теплопроводность. Преимущества и недостатки основных огнеупорных материалов приведены в Таблице 2.
Категория материала Материал Производительность Подходит для кабелей Коттоновый Аспест Канцерогенный, официально запрещен Не подходит Ультратонкая стекловата Плохая термостойкость, средняя теплоизоляция Не подходит Каменная вата Дешевый, низкий класс, низкая прочность, плохая теплоизоляция Не подходит Панельный Кальциевый силикат Высокая жесткость, плохая гибкость Не подходит Базальтовая плита Высокая жесткость, плохая гибкость Не подходит Алюмосиликатная плита Высокая жесткость, плохая гибкость Не подходит Покрытие Огнезащитное покрытие Плохая адгезия PE, низкая прочность, трещины Не подходит Войлочные материалы Войлок из базальтового волокна Средняя теплопроводность, высокая прочность, средняя термостойкость Потенциальное применение Войлок из керамических волокон Средняя теплопроводность, средняя прочность, отличная термостойкость Потенциальное применение Обычный аэрогель для теплоизоляции Низкая теплопроводность, средняя прочность, средняя термостойкость Потенциальное применение
A1. Основное огнезащитное покрытие для кабелей
Огнезащитное покрытие DreamGel на основе аэрогеля – это новый тип покрытия, изготовленный из аэрогель-материала, обладающий следующими характеристиками:
1. Низкая теплопроводность: Поры аэрогеля обычно имеют размер от 2 до 50 нм, и эта наноструктура пор значительно снижает теплопроводность. Очень низкая теплопроводность означает, что оно эффективно изолирует тепло и снижает передачу тепла от высокотемпературной зоны к низкотемпературной. При нормальных условиях температура и давление могут достигать 0,013 W/m·K.
2. Высокая теплоизоляция: Пористая структура аэрогеля предотвращает движение молекул воздуха между порами, снижая тепловую конвекцию. Эта структура также снижает тепловое излучение, что дополнительно улучшает теплоизоляцию.
3. Термостойкость: Аэрогель сам по себе является термостойким материалом, который сохраняет свою структурную стабильность даже в условиях высоких температур. Поэтому огнезащитное покрытие DreamGel может поддерживать свою теплоизоляцию в условиях высокой температуры в течение длительного времени.
4. Увеличенная прочность и адгезия материалов: С помощью регулировки формулы можно улучшить механическую прочность покрытия и его адгезию к основанию, что гарантирует целостность покрытия и его долговечные характеристики.
5. Водоотталкивающее и коррозионностойкое покрытие: Огнезащитное покрытие DreamGel обладает отличной водоотталкивающей способностью, предотвращая проникновение влаги. Увлажнение > 99%. В то же время оно обладает коррозионной стойкостью, защищая основание от химической эрозии.
6. Огнезащитные характеристики: Аэрогель сам по себе является невоспламеняющимся материалом, что улучшает общую огнезащитную способность покрытия. Когда покрытие образует слой, оно эффективно изолирует пламя от контакта с основанием, предотвращая распространение огня. Класс огнезащиты A1, класс дыма AQ1.
7. Экологичность: Огнезащитное покрытие DreamGel обычно не содержит летучих органических соединений (ЛОС), что делает его безопасным для человека и окружающей среды.
8. Легкость в применении: Огнезащитное покрытие DreamGel можно наносить с помощью обычных методов распыления или кисти, что делает его удобным и быстрым в применении. Однако важно обеспечить плотность покрытия во время нанесения, чтобы достичь лучшего эффекта теплоизоляции.
9. Широкая адаптивность: Оно может быть использовано на различных основаниях, таких как металл, бетон и другие, что делает его подходящим для различных применений в строительстве и оборудовании.
10. Удлинение срока службы: Благодаря отличным теплоизоляционным и огнезащитным характеристикам, покрытие DreamGel может эффективно защищать основу и увеличивать срок службы конструкции.
В заключение, огнезащитное покрытие DreamGel, благодаря своей отличной теплоизоляции и огнезащитным свойствам, находит широкое применение в промышленном и гражданском строительстве. Во время применения важно правильно наносить и поддерживать покрытие для обеспечения его долгосрочной эффективности.
Основы проектирования ISO12944-5:2017 Системы защитных покрытий для стальных конструкций от коррозии Среда C5 Очень высокая; внешняя: промышленные районы с высокой влажностью и суровыми погодными условиями, а также прибрежные районы с высокой соленостью Проектный срок VH Сверхдолгий Обработка поверхности ISO 8501-1 St2: Поверхность стали, очищенная вручную или с помощью электроинструментов, должна быть без видимых загрязнений и грязи, не должно быть рыхлой окисленной корки, ржавчины или слоев краски. Области покрытия Основные кабели, подвесные кабели, натяжные кабели Покрытие Тип покрытия Название покрытия Цвет Растворитель Соотношение A:B Толщина слоя (мкм) Первичный слой DreamTherm Аэрогель-огнезащитный слой DreamHeat 100 Белый / 14:0 10000 Итого 10000
-
- Решение для предотвращения обледенения канатов
-
I. Опасности образования льда на канатах моста
Канаты на моста с наклонными опорами и нижняя часть подвесных канатов на висячих мостах находятся прямо над проезжей частью. В зимнее время при низких температурах, высоких скоростях ветра и повышенной влажности канаты моста склонны к образованию льда. Образование льда на канатах моста приводит к ряду рисков для безопасности и потенциальных опасностей, включая следующие:
1. Увеличение нагрузки на канаты: Вес льда добавляет дополнительную нагрузку на канаты, особенно при большом количестве льда. Это может привести к нарушению баланса натяжения канатов и повлиять на общую стабильность и безопасность конструкции моста.
2. Снижение прочности канатов: Образование льда может изменить физические свойства материалов канатов. Например, в условиях экстремального холода некоторые материалы могут стать хрупкими, что снижает их прочность на растяжение.
3. Образование сосулек: Днём капли воды, образующиеся от таяния льда на канатах, ночью замерзают снова, образуя сосульки. Когда сосульки становятся достаточно большими или температура канатов повышается, основание сосулек может отломиться и упасть, создавая опасность для пешеходов и транспортных средств на мосту.
4. Увеличение трения: Образование льда увеличивает трение между канатами, что влияет на их нормальное движение и динамические характеристики моста, особенно когда канаты нуждаются в движении или регулировке натяжения.
5. Влияние на стабильность конструкции: Образование льда на канатах снижает общую стабильность моста, особенно в условиях сильного ветра, что может привести к усилению колебаний или раскачивания моста.
6. Увеличение стоимости обслуживания: Образование льда повреждает поверхность канатов, что приводит к увеличению частоты и стоимости обслуживания. Кроме того, наличие льда усложняет работы по обслуживанию.
7. Опасности для безопасности: Падение сосулек не только представляет непосредственную угрозу для пешеходов и транспортных средств на мосту, но и может нанести ущерб кораблям или другим объектам под мостом.
8. Влияние на внешний вид: Образование льда нарушает эстетический вид моста, особенно когда на канатах образуются сосульки. Хотя это может выглядеть эффектно, это также представляет собой угрозу безопасности.
9. Прерывание движения: Серьезное образование льда, влияющее на безопасность моста, может привести к прерыванию движения или введению ограничений, что затруднит передвижение людей. Для предотвращения этих опасностей компания Mengneng разработала технологии по предотвращению образования льда и удалению льда, включая использование углеродных нанотрубок, которые наклеиваются на канаты с суперводоотталкивающим покрытием, а также использование нагревательных кабелей и вибрационных устройств для предотвращения образования льда. Дополнительно можно использовать гидрофобные покрытия и химические средства противообледенения для уменьшения образования льда. Эти технологии покрытия Mengneng помогают повысить надежность и безопасность канатов моста в зимнее время.
II. Использование покрытия из углеродных нанотрубок Mengneng для решения проблемы образования льда на канатах
Нанесение углеродных нанотрубок на канаты моста в сочетании с суперводоотталкивающим покрытием позволяет предотвращать образование льда при помощи обогрева в условиях низких температур. Технология покрытия углеродных нанотрубок Mengneng обладает высокой электрической проводимостью и некоторым сопротивлением. Когда через углеродные нанотрубки проходит ток, из-за эффекта сопротивления выделяется тепло. Этот способ обогрева высокоэффективен и регулируем, что позволяет быстро повышать температуру канатов для таяния льда или предотвращения его образования.
2.1. Преимущества технологии покрытия углеродными нанотрубками
Технология Mengneng смешивает углеродные нанотрубки с покрытием, создавая композитный материал. Этот композитный материал может быть непосредственно намотан на канаты или вмонтирован внутрь канатов, образуя систему обогрева.
1. Высокая эффективность и энергосбережение: Углеродные нанотрубки быстро нагреваются и имеют высокую эффективность преобразования энергии.
2. Равномерный обогрев: Углеродные нанотрубки обеспечивают равномерное распределение тепла, избегая перегрева в отдельных участках.
3. Легкость: Нагревательные элементы из углеродных нанотрубок тонкие и легкие, не добавляя дополнительной нагрузки на канаты.
4. Гибкость: Элементы обогрева могут быть настроены по форме и размеру в зависимости от конкретных потребностей канатов.
2.2. Решение противообледенения Mengneng
Антиобледеняющая краска Mengneng поставляется в двухкомпонентной упаковке, состоящей из фторуглеродной смолы, пигментов, растворителей, добавок и другого компонента — алифатного изоцианатного отвердителя, предназначенного для предотвращения образования льда на поверхности или уменьшения толщины льда. Такая краска обычно обладает следующими характеристиками:
1. Низкая поверхностная энергия: Антиобледеняющая краска Mengneng имеет низкую поверхностную энергию, что затрудняет прилипание воды или льда к покрытию.
2. Суперводоотталкивающие свойства: Краска обладает суперводоотталкивающими свойствами, что значительно снижает контактную площадь между каплями воды и поверхностью.
3. Большой угол контакта: Покрытие снижает прилипание льда, позволяя льду легче соскальзывать с поверхности.
4. Низкий коэффициент трения: Поверхность покрытия имеет низкий коэффициент трения, что мешает льду прочно прилипать к поверхности.
5. Самоочищающиеся свойства: Поскольку краска предотвращает образование льда, это также снижает трудоемкость уборки.
6. Устойчивость к погодным условиям: Антиобледеняющие краски обычно имеют хорошую устойчивость к воздействию погодных условий и сохраняют свою эффективность в течение длительного времени в условиях открытого воздуха.
7. Легкость применения: Антиобледеняющую краску Mengneng можно наносить с использованием обычных методов окраски, таких как распыление или кисть.
Антиобледеняющая краска Mengneng используется в таких областях как: на поверхности воздушных судов для предотвращения обледенения и обеспечения безопасности полетов; на проводах и кабелях для предотвращения неисправностей, вызванных льдом; на мостах, дорожных знаках и других объектах для снижения рисков, связанных с образованием льда; на лопастях ветрогенераторов для предотвращения образования льда и повышения эффективности выработки электроэнергии.
Основы проектирования ISO 12944-5: 2017 Защитные покрытия для стальных конструкций от коррозии Среда C5 Очень высокая; Внешняя среда: промышленная зона с высокой влажностью и суровыми погодными условиями, прибрежные районы с высокой соленостью Срок службы проекта VH Очень долгий Обработка поверхности ISO 8501-1 St2: Поверхность гладкая и ровная Местоположение покрытия Канаты Покрытие Тип покрытия Название покрытия Цвет Совместимый разбавитель Соотношение A:B Толщина пленки μm Первый слой Материалы на основе углеродных нанотрубок Нагревательная пленка на основе углеродных нанотрубок Черный / / 0 Второй слой DreamDur Антиобледенительная краска DreamDur 660 Белый / 22.73:2.27 80 Итого 80
-
- Другие специальные подложки
-
I. Подложка с горячим цинкованием
Горячее цинкование — это широко используемый метод защиты металлических поверхностей от коррозии, при котором на поверхности стальных изделий образуется слой сплава цинка и железа для защиты.
Основание дизайна ISO12944-5:2017 Системы защитных покрытий для стальных конструкций от коррозии Среда C5 Очень высокая; внешняя: высокая влажность и суровые погодные условия в промышленных районах и прибрежных зонах с высокой соленостью. Срок службы VH Очень долгосрочный Обработка поверхности ISO 8501-1 St2: Поверхность стали должна быть свободна от видимых жиров и грязи, и на ней не должно быть рыхло прикрепленных оксидных пленок, ржавчины или слоев краски. Область нанесения покрытия Вкладыши с горячим цинкованием, ограждения, столбы Покрытие Тип краски Название краски Цвет Совместимый растворитель Соотношение A:B Толщина пленки, мкм Первый слой DreamCover Специальный грунт для цинкования DreamCover 221 Светло-серый, полуглянец Эпоксидный растворитель DreamThinner 17 25:5 280 Второй слой DreamDur Акрилово-полиуретановая краска для финишного покрытия DreamDur 550 Индивидуальное смешивание цветов по национальным и международным стандартам Полиуретановый растворитель DreamThinner 10 21.4:3.6 80 Всего 360 II. Подложка из нержавеющей стали
Нержавеющая сталь сама по себе обладает хорошими антикоррозионными свойствами, но в некоторых случаях необходимы дополнительные защитные меры для повышения её долговечности и эстетичности.
Основание дизайна ISO12944-5:2017 Системы защитных покрытий для стальных конструкций от коррозии Среда C5 Очень высокая; внешняя: высокая влажность и суровые погодные условия в промышленных районах и прибрежных зонах с высокой соленостью. Срок службы VH Очень долгосрочный Обработка поверхности ISO 8501-1 St2: Поверхность стали должна быть свободна от видимых жиров и грязи, и на ней не должно быть рыхло прикрепленных оксидных пленок, ржавчины или слоев краски. Область нанесения покрытия Вкладыши из нержавеющей стали, ограждения, столбы Покрытие Тип краски Название краски Цвет Совместимый растворитель Соотношение A:B Толщина пленки, мкм Первый слой DreamCover Специальный грунт для нержавеющей стали DreamCover 221 Светло-серый, полуглянец Эпоксидный растворитель DreamThinner 17 25:5 280 Второй слой DreamDur Акрилово-полиуретановая краска для финишного покрытия DreamDur 550 Индивидуальное смешивание цветов по национальным и международным стандартам Полиуретановый растворитель DreamThinner 10 21.4:3.6 80 Всего 360
-
- Техническое обслуживание мостов: анализ отказов / основы / выбор покрытия
-
I. Анализ отказов антикоррозийных покрытий
Отказ антикоррозийных покрытий означает деградацию различных физических и химических свойств покрытия после длительного воздействия агрессивной среды, в результате чего оно теряет свои первоначальные характеристики и частично или полностью утрачивает защитную функцию для основания моста.
Отказ антикоррозийных покрытий моста можно разделить на две основные категории: отказ органических покрытий и отказ металлических покрытий.
1. Анализ отказа органических покрытий
Основной причиной отказа является воздействие химических веществ на покрытие или длительное воздействие внешней среды, такой как ультрафиолет, дождь с колебаниями температуры, а также набухание и диффузия коррозионных агентов, приводящие к разрушению покрытия.
2. Анализ отказа металлических покрытий
Для металлических покрытий, таких как горячее цинкование, горячее алюминирование, горячее оцинкование и покрытия с высокой концентрацией цинка, которые используют катодную защиту цинка или алюминия в процессе эксплуатации, самопожертвование для защиты стального основания, отказ покрытия проявляется в виде равномерной химической или электрохимической коррозии. Срок службы покрытия можно рассчитать, основываясь на скорости коррозии, полученной из экспериментов, и, зная толщину покрытия, вычислить срок его службы. Коррозионный отказ покрытий с высокой концентрацией цинка совмещает характеристики как органических, так и металлических покрытий. С одной стороны, такие покрытия обеспечивают катодную защиту стали, с другой стороны, отказ органического покрытия может привести к потере сцепления или отслаиванию цинковых частиц, что снижает их эффективность. Поэтому срок службы покрытия с высокой концентрацией цинка зависит от того, какой из этих факторов является доминирующим.
3. Отказ композитных покрытий
Современные системы антикоррозийной защиты мостов включают в себя комбинированные покрытия, сочетающие металлические и органические покрытия. Внешнее органическое покрытие эффективно блокирует воздействие коррозионных факторов на металлическое покрытие и сталь. Отказ композитного покрытия начинается с отказа внешнего органического покрытия, что чаще всего проявляется в виде порошкообразования или отслаивания. Из-за повреждения органического покрытия коррозионные агенты могут проникнуть на поверхность, что приведет к разрушению металлического покрытия. Накопление коррозионных продуктов также приведет к снижению адгезии органического покрытия.
II. Основания для ремонта покрытия
В связи с коррозионным отказом антикоррозийных покрытий необходимо в определенный период обновить и обслужить первоначальное антикоррозийное покрытие для обеспечения безопасности и долговечности моста. Но на каком основании происходит обновление и обслуживание? Проще говоря, как определить степень отказа первоначального покрытия моста—частичный или полный? При этом, как обеспечить более экономичное и рациональное решение, когда необходимо обновление и обслуживание моста?
Стандарт GB/T 1766-1995 «Цветные краски и лаки. Методика оценки старения покрытий» (ссылаться на ISO 4628/1-5-1982) предоставляет подробную методику оценки. Оценив пузырьки, ржавчину, трещины, отслаивание органических покрытий, можно оценить степень их коррозионного отказа, что является ясным основанием для разработки планов обслуживания для соответствующих органов управления.
Согласно указанному стандарту, обычно считается, что когда общее значение степени отказа органического покрытия достигает 3 (S3) или 4 (S4), необходимо как можно скорее произвести обновление и обслуживание покрытия.
Важно уточнить, что «ржавление», упомянутое в стандарте, происходит из-за неправильной обработки поверхности основания, недостаточной толщины покрытия или неправильного нанесения покрытия, а также наличия отверстий и проемов. Ржавление означает, что покрытие в определенных местах полностью утратило свою защитную функцию, что также влияет на общую антикоррозийную эффективность органического покрытия. Накопление коррозионных продуктов в местах ржавчины ускоряет процессы пузырькообразования, отслаивания и старения на окружающих участках покрытия. По мнению специалистов в области антикоррозионных технологий, когда площадь ржавчины достигает уровня 3 (соответствующего Ri 3 в ISO 4628/3 или Re 3 в европейских стандартах), покрытие должно быть отремонтировано. Таким образом, для мостовых конструкций, когда на верхнем слое краски появляется порошкообразование 3-го уровня и его толщина уменьшается более чем на 50% от первоначальной, или когда это требуется для декоративных целей, необходимо полностью очистить поверхность и нанести совместимую краску (1-2 слоя). Если покрытие имеет трещины 2-3 уровня, отслаивание 2-3 уровня или пузырькообразование 2-3 уровня, но грунтовка в хорошем состоянии, следует применить соответствующие промежуточные и верхние покрытия. Когда покрытия имеют ржавчину уровня Ri2-Ri3, необходимо тщательно очистить поверхность и нанести соответствующие грунтовые, промежуточные и верхние покрытия.
III. Проектирование и строительство ремонтных покрытий
Разработка плана ремонта покрытия для моста гораздо сложнее, чем разработка покрытия для нового моста. Требуется системный подход и проведение определенных испытаний для определения состояния исходного покрытия и целостности всей конструкции. В то же время необходимо тщательно изучить условия施工, связанные с экологией, безопасностью и законодательством, чтобы выработать целенаправленный ремонтный план.
IV. Выбор красок для ремонтных покрытий
Прежде чем выбирать краски для ремонта, необходимо провести всесторонний анализ первоначального покрытия. Это включает в себя состояние адгезии покрытия и анализ системы покрытий. Простые полевые испытания могут дать общее представление о состоянии покрытия. Например, метод разрезания (GB/T 9286-1988) позволяет быстро определить адгезию (между покрытиями, внутри покрытия или между покрытием и основанием). Тест на стирание MEK помогает определить, является ли покрытие физически высыхающим, окисляемым или химически твердеющим. Эти тесты дают грубые результаты и могут служить только ориентиром. Для точных результатов необходимы другие методы или лабораторные тесты.
Кроме того, необходимо учитывать требования к обработке поверхности, условия работы на объекте, а также оборудование и технику нанесения покрытия.
На основании этих тестов и анализов, а также с учетом совместимости покрытий и срока службы проектного покрытия, можно выбрать подходящие краски для ремонтного покрытия.
V. Строительство ремонтных покрытий
В зависимости от степени старения исходного покрытия, можно выбрать частичный ремонт или полное обновление покрытия. Для частичного ремонта можно использовать простые ручные или моторные инструменты для обработки поверхности поврежденных участков и применять роликовое, кистевое или распылительное нанесение для ремонта. Для полного обновления необходимо полностью удалить старое покрытие и провести соответствующую обработку поверхности (обычно пескоструйную обработку), после чего нанести новое антикоррозийное покрытие в соответствии с требованиями строительства нового моста.
-
Просмотр в деталях
We don't know where to start.
-
Миниатюрный просмотр
Как выбрать правильный тип покрытия?
-
ISO 12944 — это стандарт для защиты от коррозии стальных конструкций с помощью красок, который определяет коррозионную среду, срок службы антикоррозийного покрытия, соответствие краски и толщину пленки.
Corrosion factors are numerous and varied.
-
Выбор
Как решить проблемы отрасли с помощью покрытий?